Flash Battery has launched its new laser-welding automated module meeting line.
The results of an funding of over €6 million, the brand new line is the core of the corporate’s current headquarters enlargement which added 2,200 sq. metres devoted to a completely automated space for battery module meeting.
With an annual manufacturing capability reaching 90,000 modules, this division is designed to deal with all the welding and mechanical integration course of inside a managed surroundings.
Flash Battery has chosen to internalize and develop all key course of abilities inside its HQ: from its proprietary battery administration system to mechanical and electrical design, course of validation, and predictive upkeep.
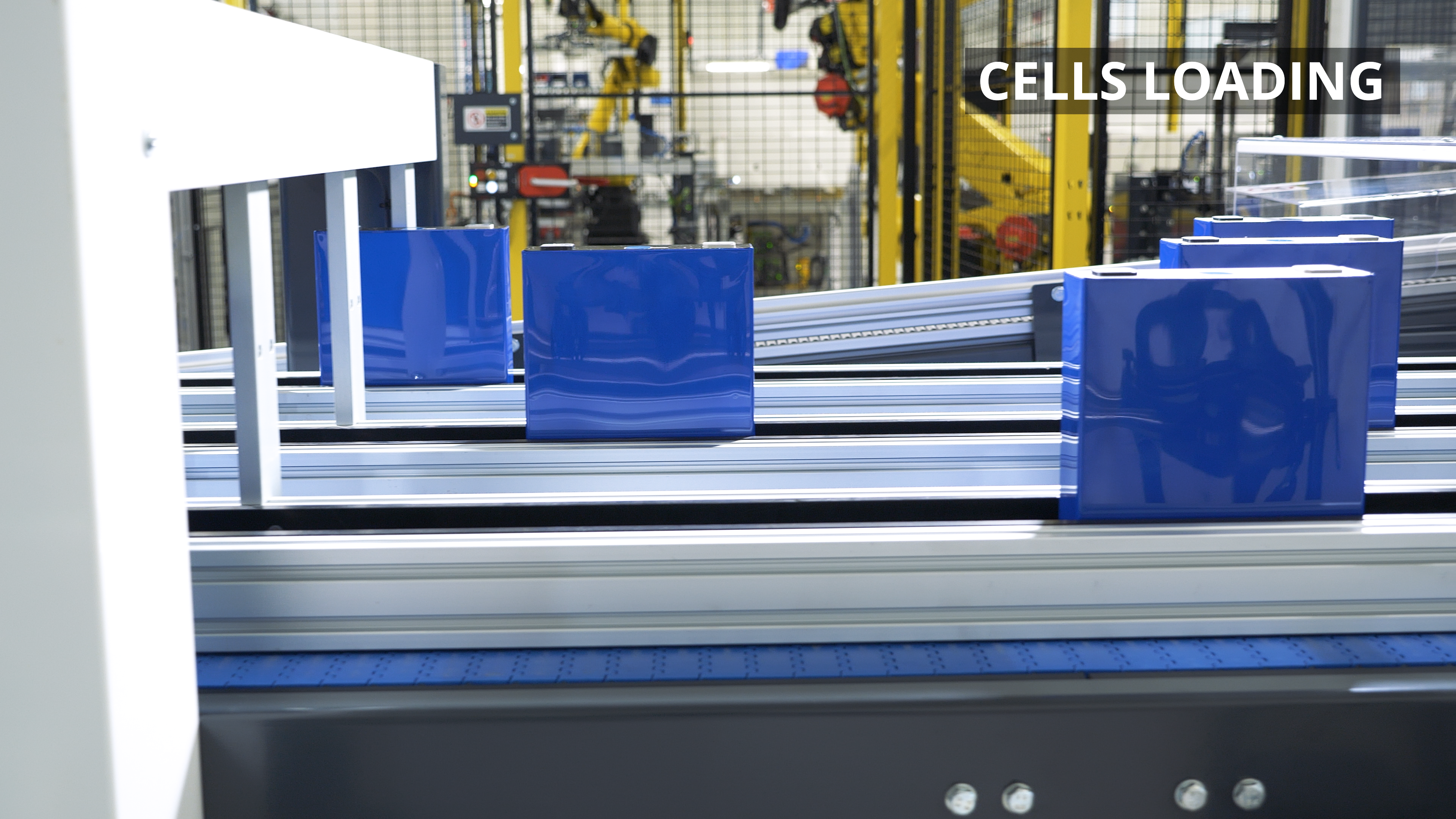
With the combination of this new module meeting line, the corporate finalizes its in-house manufacturing consolidation course of, now additionally instantly controlling welding and meeting actions beforehand outsourced to exterior suppliers. Aside from the cells – sourced from high international producers – each part is now managed and supervised instantly by Flash Battery.
This built-in administration mannequin permits the corporate to ship totally tailor-made options aligned with every buyer’s software wants, sustaining constant requirements of high quality and efficiency, even in complicated and dynamic industries.
“Bringing battery module meeting in-house means going on to the supply of the provision chain,” says Marco Righi, CEO and founding father of Flash Battery. “For cells, we depend on main international suppliers, choosing a number of suppliers for every kind to extend provide chain reliability and improve our negotiating energy. Current geopolitical and financial developments have confirmed the significance of getting direct management over manufacturing to cut back lead instances and provide points.”
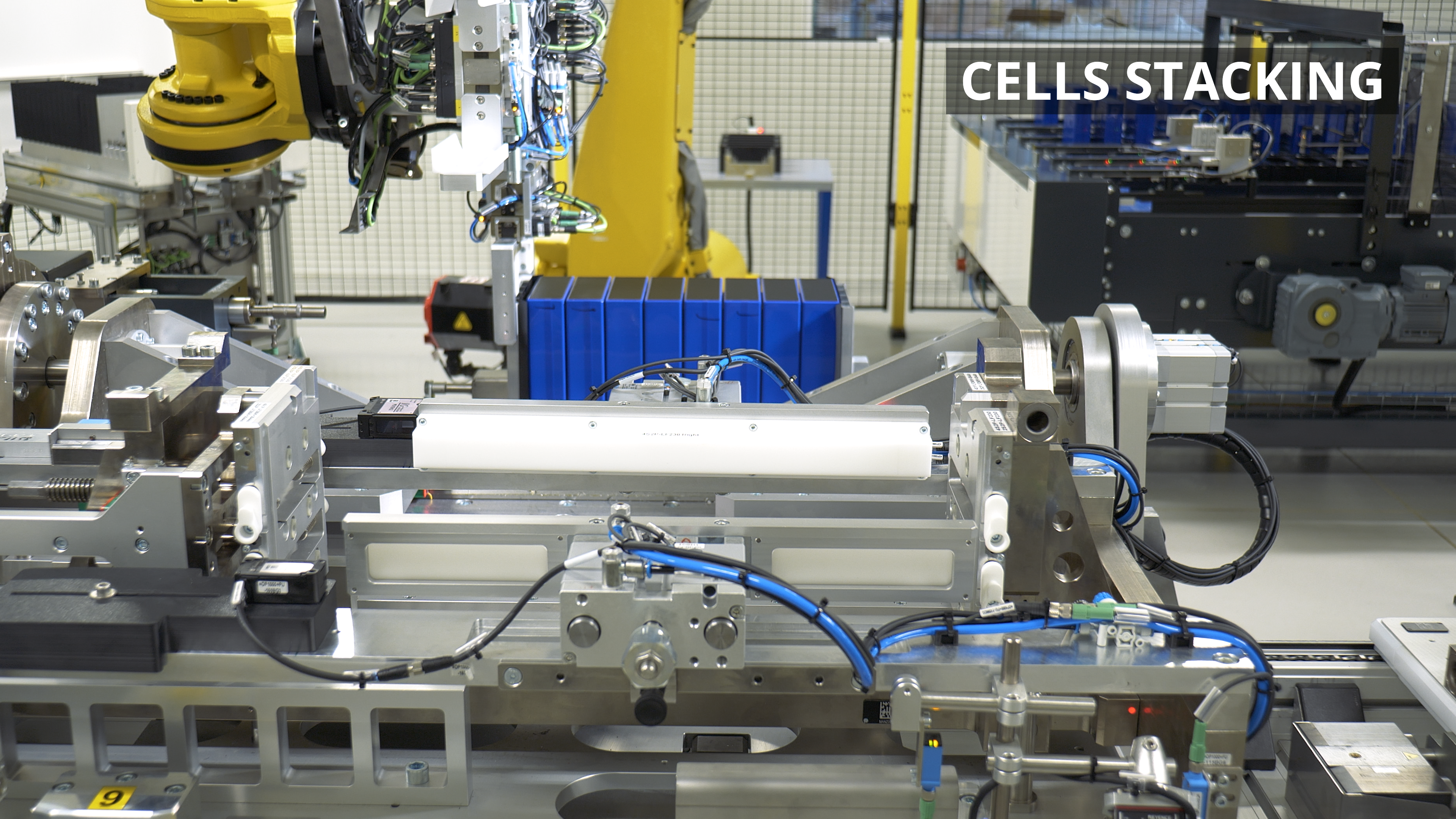
The brand new meeting line is engineered to shortly swap between configurations, managing 13 module variants with changeover instances of lower than 10 minutes. This allows Flash Battery to reply shortly and precisely to even essentially the most particular buyer necessities, supporting the creation of optimized electrical programs with out compromising on time or high quality.
Laser welding ensures stronger mechanical and electrical joints, larger resistance to vibrations and decrease vitality dispersion. That is important for reaching secure and dependable efficiency, significantly in demanding industrial functions.
The road operates by way of 4 core automated phases. The primary is cell loading and automatic inspection utilizing optical inspection programs and high-precision sensors. Subsequent is module formation with robotic stacking and placement of parts right into a containment construction for subsequent welding. Then, laser welding of frames and bus bars join the cells for a sturdy and environment friendly electrical connection. Remaining compliance testing embody security, insulation, and mechanical resistance exams. Solely modules that go all exams are labelled and despatched to Flash Battery’s battery pack meeting strains.
“With this new line, we’re taking a decisive step towards a extra autonomous, environment friendly, and dependable manufacturing mannequin,” provides Marco Righi. “Integrating manufacturing abilities permits us to reply promptly to buyer wants and ship tailor-made options with top-tier high quality and efficiency. This can be a key aggressive benefit in a consistently evolving market.”
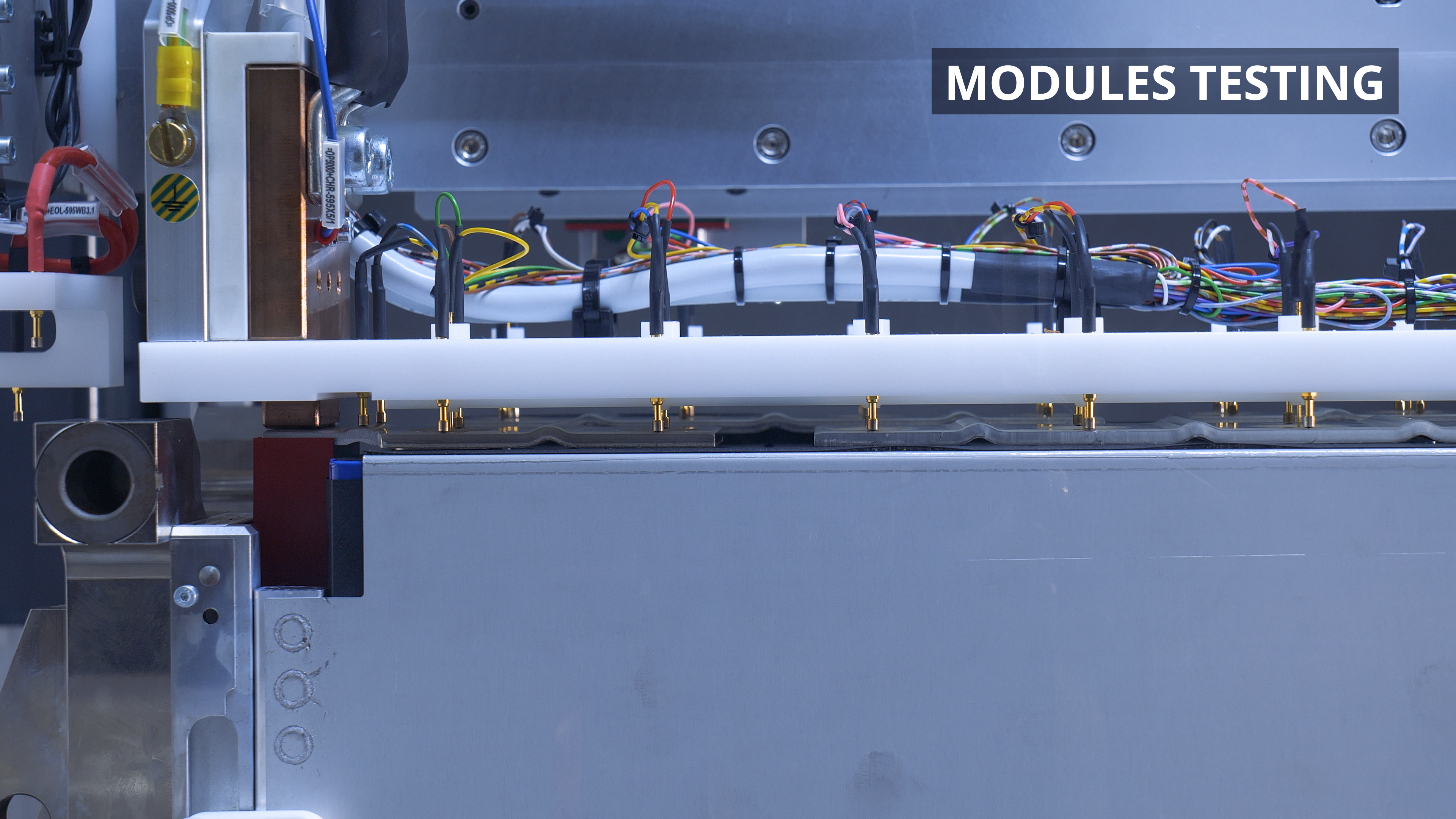
With this sturdy in-house autonomy, and the upcoming launch of European gigafactories devoted to LFP (Lithium Iron Phosphate) cell – a protected, secure, and cobalt-free lithium know-how – Flash Battery will quickly be capable to provide prospects a completely European provide chain.
Photos courtesy of Flash Battery